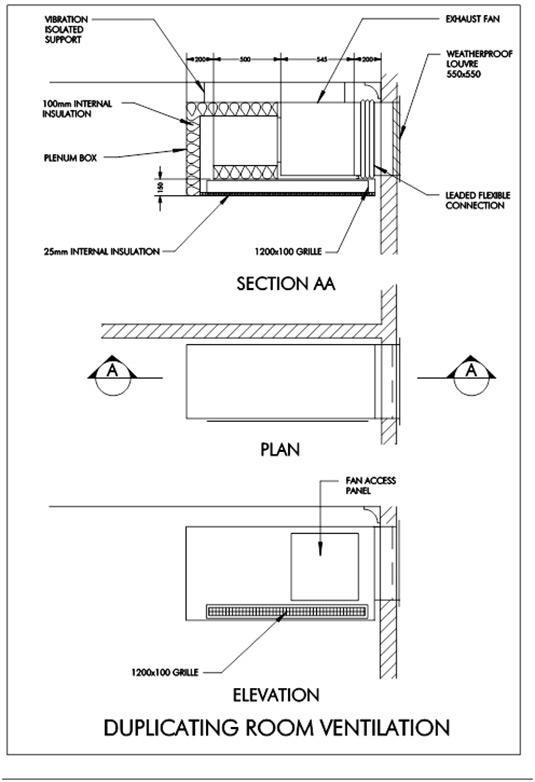
A ventilation strategy must be developed to ensure that sufficient ventilation is provided to all spaces to meet the requirements of the BCA/NCC and associated standards.
Each room and space must be categorised as required by the BCA into the associated groups, including:
The need for ventilation equipment must be minimised by employing passive sustainable design principles (eg. good natural ventilation, rotary ventilators etc).
Where active ventilation systems are required, they must be designed from a “Whole of Life” (WOL) perspective to provide:
Specifically ventilation equipment must :
The ventilation systems may include any or all of the following:
The installations must comply with the requirements of the BCA/NCC and related standards.
As part of the design process the following documentation will be required for all jobs:
Provide construction and work-as-executed drawings in industry recognised DWG CADD file format as well as PDF format.
All drawing sets shall include:
Equipment schedules (NTS)Drawings shall be drafted in CAD file formats approved by DoE.
Ensure effective co-ordination between disciplines. Organise the information from all sources to meet a set programme.
At sketch plan stage:
Equipment Life-Cycle Cost Calculations
For new schools and when replacing or updating major ventilation system components, a simple life-cycle cost should be calculated. This should be based on the Life Cycle Cost considerations following over a period of time, e.g 20 years and/ or the life of the asset.
As part of the Whole of Life analysis, the life cycle costs must consider the following:
The following should also be considered:
Design Conditions
Refer to DG / ACOUSTICS
General
A ducted dust extraction system is required in materials handling learning areas within secondary schools. This system transports the fine air-borne wood particles from the work face via ducting to a dust extraction unit, where they are separated from the air and collected.
Consideration should be taken of noise at the boundary.
References
The areas and machines to be treated are stipulated in the Secondary EFSG.
Refer to Secondary EFSG
Dust Extraction Space
Provide a separate Dust Extraction space adjacent to Materials Workshop Type 2 and Materials Workshop Type 3 if required
Minimum clear internal dimensions are 1800 mm (depth) x 3600 mm (wide) x 3500 mm (height).
Construct enclosure to provide noise isolation, protection from vandalism and weather protection.
Door opening to be central to the enclosure. Door opening to be minimum 1800 mm and height to be as high as the machine, minimum door height 2040mm.
Refer Secondary EFSG
To improve the noise attenuation of the surrounds to the dust extraction unit:
Air Relief
“Cleaned air” to be discharged to atmosphere.
Door-Access and Security
Lock to be PW “E” keyed.
Access and Floor Levels
External access to the Dust Extraction space is preferred with no change in floor level at point of access, for maintenance purpose.
Minimum acceptable floor finish: broom swept concrete graded to door
Ceiling Levels
Avoid excessive difference in ceiling levels between Dust Extraction space and Materials Workshop in order to minimise bends, and so reduce pressure drop.
Machines for Dust Extraction - New School
Machines are nominated and supplied by the school. Liaise with DoE Project Director for the type and number.
A single dust extraction point can be used for air from a Disc Sander and Bandsaw, as generally both units will not be used at the same time.
Provide for a future (air shared) extraction point in the Machine Zone in each Materials Workshop Type 2 and Materials Workshop Type 3 if required.
Ductwork
Use circular high pressure fully welded pre-fabricated metal ductwork and fittings. Ductwork must be demountable by the use of quick couplings suitable for sawdust extraction. To reduce air pressure drop, co-ordinate the grouping of machines to provide a balanced layout to assist duct design and to eliminate unnecessary long ductwork. Ensure that there is a least 400mm clearance between rear-side of lathes and adjacent partition or wall. Confirm the type and model of each wood machine in order to ensure the correct hood design.
Run ductwork clear of ceiling by 50-100 mm. Avoid ducts running directly in front of ceiling lights. If surface mounted or recessed lights are present, provide sufficient clearance to enable diffuser and fluorescent tube removal.
The aim of the layout is to achieve a balanced, equal resistance design, and minimise the static resistance whilst achieving acceptable internal noise levels.
Verify that ceiling or wall structures do not conflict with duct penetrations and duct runs (it is essential to avoid sudden changes in direction of ducts for materials handling). Check head height clearances from ductwork if structural beams force ductwork to be lowered.
Air Relief
Heating
Where heating is necessary, use only ducted warm air heating or low surface temperature heaters.
Instruction Labels and Signage
Provide labels and signage to instruct the user in the operation and general maintenance of the system. Specify the appropriate labels from the Standard Instruction Label Sheet for inclusion in the project.
Controls
Provide remote “stop-start” controls in each of the spaces served by the unit.
Modern dry photocopiers are designed for low emissions, provided they are properly maintained (including replacement of the ozone filter). The ventilation system is to be designed to serve the whole room and is not intended to provide localised exhaust at equipment.
Provide ventilation systems to meet the following performance requirements in new photocopier and printing rooms:
DUPLICATING/ PRINTING ROOM VENTILATION (cont.)
Provide separate system for each fume cupboard. The ventilation system to strictly comply with AS 2243.8 (Safety in Laboratories Part 8: Fume cupboards). Fume cupboards are to be located clear of openings and corners as required in the standard.
Exhaust Fans
UPVC Construction. The following types of fans, may be used:
The Mechanical Engineer is to advise on the type of installation to be used. All exhaust fans are to be installed outside and supported from the building. Provide safe access for service of all fans as required for compliance with WH&S
Fans are to run continuously whilst class is in use and fan speed is to vary to provide exhaust volume control depending on sash height of fume cupboard
System to maintain a constant air velocity at the fume cupboard opening
Ductwork
Use equal friction method for duct sizing with 1 Pa/m maximum pressure drop or 5 m/s maximum air velocity.
Ductwork design to comply with AS 4254.
Materials: UPVC or Special Grade Stainless Steel
Ductwork is to run outside the building well clear of any air inlets. Ductwork should follow the most direct route from the cabinet/cupboard to a point of discharge keeping bends to a minimum.
The discharge position and arrangement are to comply with AS 2243 part 8
Minimise horizontal duct runs and if unavoidable, slope duct towards a drainage point.
Drainage
Connect a permanently plumbed-in drain of 50 mm UPVC pipe to the lowest point of the fan casing to permit disposal of condensate. To prevent recirculation of fumes, the drain is to incorporate a water seal or P-Trap.
Introduction
Provide mechanical exhaust system with high and low level exhaust points to all chemical stores, with a minimum of 15 air changes per hour flow rate.
Air Discharge
Discharge air according to the requirements of BCA. The discharge outlet is to be fitted with bird wire mesh.
Fresh Air Intake
Provide make up air to all chemical stores, (to replace exhausted air) through openings in an external wall, fitted with weatherproof louvres. All grilles and louvres are to be fitted with vandal proof bars and be fitted with vermin mesh.
For security and fire rating reasons do not use windows/doors or door grilles for air intake.
Control
The Chemical stores ventilation systems are to run continuously.
Ductwork
Use equal friction method for duct sizing with 1 Pa/m maximum pressure drop or 5 m/s maximum air velocity.
Ductwork design to comply with AS 4254.
Ductwork to be bracketed against or close to wall and allowance to be made for a 150 x 150 mm dropper. Provision to be made for dropper to penetrate shelving to 100 mm from floor for low level exhaust intake.
The following diagram shows a typical Chemical System installation
Diagram of Chemical Store Ventilation
1. Low Level Exhaust.
2. High Level Exhaust.
3. In-Line Centrifugal Fan.
4. Alternative Roof Mounted Vertical Discharge Exhaust Fan.
5. 2 Hour Fire Rated Enclosure for Duct to Roof Mounted Fan.
6. Alternative Vertical Discharge Cowl.
7. Control Switch.
8. Air Inlet Louvre in External Wall.
Where open mesh walls are provided in accordance with EFSG, mechanical ventilation is not required.
A mechanical exhaust system must be used in the following situations:
Install a separate stainless steel hood and stainless steel fan above each kiln. Stainless steel sheet metal ductwork must be used for kiln exhaust system.
Refer to the ASHRAE Handbook for guidance on the face velocity at the hood.
The general arrangement is described below.
Exhaust Fans
Exhaust fans may be vertical discharge mixed flow roof extract types or duct mounted axial flow type. Axial flow type fans are to be installed above the roof and fitted with a weatherproof vertical discharge cowl. Ensure fans or other equipment are located in positions where safe roof access has been provided for maintenance.
Air Discharge
Discharge air according to the requirements of BCA.
Discharge to be vertical above roof and well clear of any adjacent building to avoid corrosion by the fumes extracted from the exhaust fan. The discharge outlets is to be fitted with stainless steel bird wire mesh.
Controls
For each kiln exhaust fan provide an on-off switch with red indicating light and labelled “gas fired/electric/No.1 kiln exhaust fans”, as applicable.
Provide galvanised steel exhaust hood over all hot metal workstations to remove the fumes and hot air.
Where hot metal and welding share the same area provide separate ventilation for each service.
Exhaust Fan
Use in-line duct-mounted exhaust fan, or a roof-mounted exhaust fan providing that all necessary safety precautions are implemented and safe access is provided for maintenance.
The fan is to be sized to ensure a uniform air velocity of 0.6m/s across the face of the hood.
Air Discharge
Discharge is to be vertical above roof and well clear of any building openings in accordance with the BCA/NCC.
Exhaust ducts that pass through floors and rooms above are to comply with the fire-rating protection requirements in the BCA/NCC.
Fresh Air Intake
Provide for make up air to enter the workshop, to replace the exhaust air. A weatherproof and vermin-proof grille suitably sized and fitted to an external wall/window is required.
Controls
Provide a fan on-off control with a 0-4 hour run-on timer, located near the workstation.
Introduction
Where dark rooms are included, a ventilation system will be required to provide safe and satisfactory working environment as required by AS. The system is to:
Fresh Air Supply
Adequate filtered fresh air supply is essential in controlling both temperature and fume exhaust.
Supply air is to be from a source external to the building in accordance with the BCA/NCC.
Exhaust Air
Ensure that the dark room has a general exhaust system giving the rate specified in AS1668.2 but no less than a minimum of 15 air changes per hour as well as local exhaust to cover fume emissions.
Discharge the exhaust system vertically to the outside of the building in accordance with the BCA/NCC.
Use in-line duct-mounted exhaust fan, or a roof-mounted exhaust fan providing that all necessary safety precautions are implemented and safe access is provided for maintenance.
Ducts that pass through floors and rooms above require fire-rating protection in accordance with the BCA/NCC.
Local exhaust should be at the source of fume emissions. Use side draft plenum type with horizontal exhaust slots 150 mm above the source. The slots are to have an air velocity of 10-12 m/sec at the face and 0.6 m/sec at 450 mm from face of slot.
Ductwork
Use equal friction method for duct sizing with 1 Pa/m maximum pressure drop or 5 m/s maximum air velocity.
Ductwork design to comply with AS 4254.
Both Air Supply and Exhaust systems shall be designed in accordance with noise levels noted in DG / ACOUSTICS.
Light Transmission
Ensure that external light does not enter the dark room. All penetrations or openings into the dark room are to be sealed or designed so that light penetration is not possible. All fittings are to be light-proof.
Heating
Provide temperature control to avoid unwanted chemical reactions, by heating the supply air system. Control the supply air temperature by a room thermostat.
Controls
Controls are required as follows:
The controls shall be located within the room. Location to be decided by the Architect.
Provide mechanical exhaust points adjacent to each welding workstation.
Where welding and hot metal share the same area provide separate ventilation for each service.
Exhaust Point
Air Discharge
Fresh Air Intake
Ductwork
Control
The fan on-off control is to be located near the workstation, subject to the approval of the Design Architect.
School buildings can use wind powered roof ventilators with dampers to provide effective summer ventilation. Design to suit local ambient climatic conditions to ensure correct sizes, locations and numbers are provided for each particular application. Refer to manufacturer’s specification’s for assistance in system sizing according to various wind velocities.
Co-ordinate the locations of ventilators with the ceiling fans to achieve effective air movement.
Fan assisted ventilators should also be considered on days of low wind
Provide a wall mounted switch to open /close the damper.
Where there is a risk of gas build up in a cupboard enclosing a gas service, (e.g. under a gas cook top and especially with LP gas), ensure the cupboard is adequately vented by way of solid metal grilles/vents in at least one side at the top and bottom.
Ensure ventilation rate and design is in compliance with the gas code AS5601 and ventilation AS1668.2.
Where bottled gases are used, their enclosure is to comply with relevant codes and standards.
DG57/1 Roof Ventilators - Damper Operation- Switch